Living flame gas fires have proved to be a popular choice for heating within the home for a number of decades – however, their design and appearance has moved on immensely since their rapid rise in popularity during the 1980’s and 90’s. Superior levels of realism, controllability and efficiency can be contributed to contemporary features, such as battery powered thermostatic remote controls with automatic electronic flame safety.
The first attempts at gas fires that resembled real flames, focussed on the 16” wide open coal fire found in millions of homes countrywide. These fires were lit with a match, often had no pilot or any safety devices, gas consumptions were large and complaints about high gas bills combined with little room-warming output were rife.
Safety was also not a major concern in the early days – although that quickly improved with the introduction of piezo ignition, then flame-failure devices, and subsequently spillage monitoring devices, which became mandatory during the 90’s.
During the 1980’s and 90’s, improvements were made to the combustion efficiency obtained from 16” coal effect yellow flame fires, by producing burners that at least partially aerated the gas being burned before it was released. This coincided with the rapid developments in the forming of realistic fuel shapes from ceramic fibres.
Stainless steel burners began to be adapted and sometimes designed specifically for gas fires, and special aerated burners of every variety were designed in bespoke shapes and configurations to give a tailored flame that could be used to heat the centre of a ceramic fibre bed to temperatures in excess of 1000 degrees Celsius.
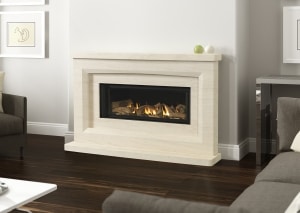
The Infinity 890FL Brockton suite from Charlton and Jenrick Ltd
During the 1980’s a variety of hearth standing gas fires became popular through British Gas, which sought to give the customer an efficient version of the living flame fire. Whilst these were typically 60% efficient, they had a relatively unrealistic appearance, with an extremely obvious glass front.
As burners continued to be developed, it was quickly realised that part of the efficiency problem was the fireback surrounding the open fronted gas fire. Refractory ‘Milner’ fire backs were very tough and adequate for radiating coal fire heat, but didn’t restrict the draught up the chimney enough, and needed to radiate more efficiently for gas. This problem was resolved with the introduction of a lining of ceramic fibre inside a metal convector or radiant box.
Finally an open fronted fire was producing efficiencies around or in excess of 50% – better than an open fire at approximately 20% but slightly less than hearth standing glass fronted gas fires of about 60%.
During this time, British and European standards had developed rapidly, which meant safety took a big leap forward. Installers became strictly controlled through UK law, which means that today you are much more likely to have a successful and safe gas fire installation experience.
With the property building, development and improvement boom during the 2000’s, people began to look much further than the traditional coal fire for something to provide a realistic and convenient live fire feature in their homes.

The highly efficient Infinity 880FL in the Regency style Rembrandt suite with black liners and fire basket.
A trend for open fronted ‘hole in the wall’ gas fires emerged, however this was not to last. It had become obvious through pioneering inset glass fronted fires that a consumer could have a really efficient inset gas fire that was both great to look at and didn’t lose heat up the chimney by having an open front.
This technology was applied to bigger and better fires that formed the centre point of a room. Gone was the traditional 16” wide limitation, and in it’s place were large format European gas fires. Although not tailored to the UK market, and in most cases very difficult and costly to install, they began to sell in larger quantities for the first time.
So the gas fire had finally come of age, an efficient, glass fronted inset fire with a realistic flame and fuel effect which could either be built into the wall or alternatively built in to a bespoke fireplace package….. Or had it? Early UK large format gas fires were often EU fires, or copies, usually with a balanced flue, and requiring their own flue system and air supply and a great deal of building work
Energy price rises across the board meant that high gas consumptions for big flames were now something of the past. As a result, fires were designed that could be fitted into existing properties with relatively small amounts of building work and that maximise the flame picture from lower gas inputs.
Upper end gas fire remote control systems are steadily improving in terms of usability, features and energy consumption. Modern fires of this type are usually equipped with battery operated remote controls to maintain the advantage of fuel autonomy that a gas fire can bring. In a power cut a central heating boiler is useless whereas an autonomous gas fire can continue to be used to provide vital heating in living spaces. Thermostatic controls can be used for reduced gas consumption whilst maintaining comfort levels without switching on the whole house heating during the warmer months.
When looking at the past few decades of gas fire development, it is incredibly apparent how far things have come on terms of aesthetic satisfaction, ease of maintenance and installation, and economic efficiency, and there is no doubt that the gas fire remains relevant today.
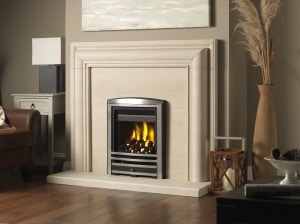
Rembrandt Limestone Fireplace
Charlton & Jenrick Ltd are leading manufacturers and suppliers to the fire. fireplace, and stove industry. We have five industry leading brands – these are Katell, Paragon, Matchless, Fireline, and Infinity Fires. We supply local independent showrooms, local government (social housing), high street retail chains, and nationwide house builders. As a group, we are committed to the research and development of highly efficient, environmentally friendly, innovative, and attractive products for the fire, fireplace, and stove industry. We are ISO 9001 and 14001 accredited.
Please contact us for more information about our range of gas and electric fires, along with our wood burners too.